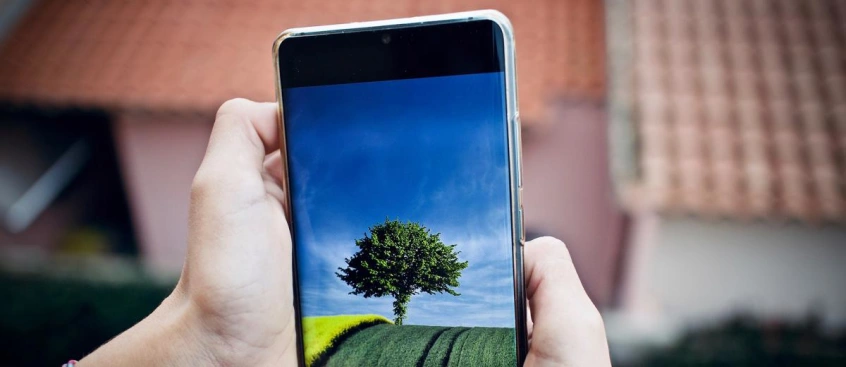
Buying AgTech Online
Dec 13 2024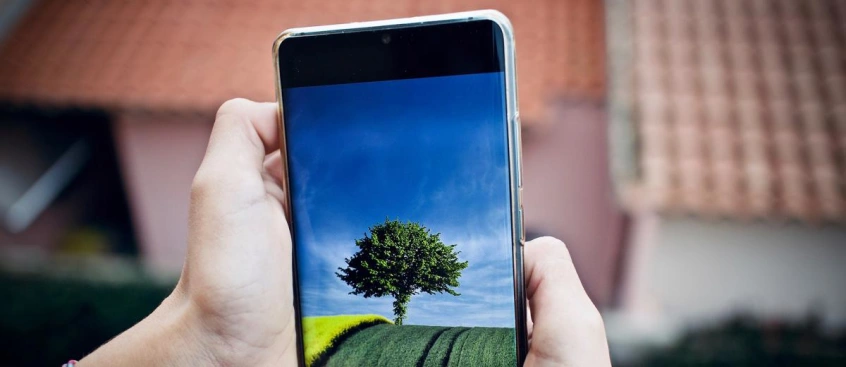
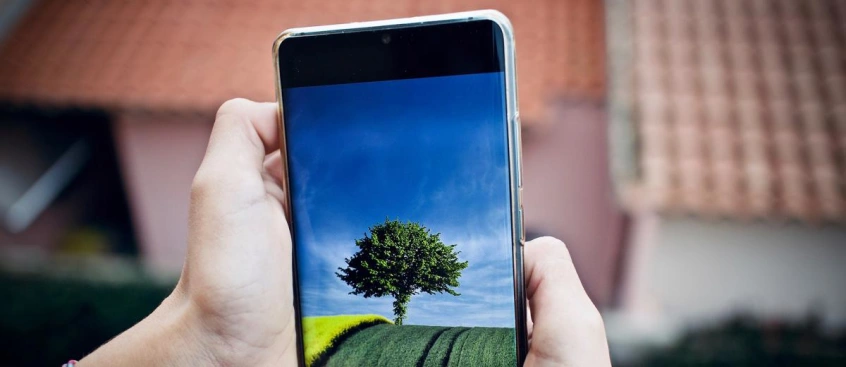
AgTech equipment, sensors, monitoring gear and all the accessories can be a bit of an investment, and every piece is an important piece of a much larger puzzle. If you’re buying agtech equipment, online be prepared for a few little hiccups along the way, but don’t let these turn you off. Landing the right equipment isn’t as easy as having a bag of fertiliser delivered from the Co-op.
Here are a few things to keep in mind if you’ve placed an order for some new equipment online.
Is the Equipment from the OEM?
Is the equipment an original factory product and from an Original Equipment Manufacturer (OEM)? Many vendors sell products of other companies or have accessory parts and equipment that they market for other manufacturers.
This is especially important when buying replacement parts and consumables e.g. batteries, filters, oils and even tools used to facilitate repairs. Also, if you’re not planning on buying the maintenance and consumable parts from the original equipment manufacturer, then this may void your warranty or reduce the performance or life of your agtech.
Is the product new? Is the box sealed? Some products come in a box, others might be delivered out of the box but with the software or integrations that you requested already wired in. What is worth emphasising is that however the product or equipment arrives – does it meet your expectations? If it doesn’t, contact the seller immediately and discuss a more suitable solution.
Did Your Delivery Arrive Safely?
Has the equipment been damaged in transit? Sometimes the damage may not be visible, so it is important to test your equipment when it arrives instead of putting it on the shelf and hoping it works the day you need it.
A damaged box is a definite watch out and shows that the product inside has been knocked and dropped (another reason to check that what has been delivered works).
Does the equipment exhibit structural damage like fractures or cracks? Protective casings are not bullet proof (unless, of course, their specification sheets say they are!), so even if a piece of equipment is meant to be able to take a few knocks, be wary if any protective casings are scratched. If any of the casings are cracked in any way, then don’t accept the goods as there’s a chance moisture, dust or other nasties may have made their way inside and could cause issues at a later date.
Is your product safe to turn on?
Are there any proofs of safety and reliability tests of the product?
If the product is manufactured overseas then you need to ensure the power cords, power supply boxes, chargers, transformers, and any other pieces that have electricity running through them have been certified for use in Australia. This will need to be done by a licensed electrician. There are no shortcuts here. Don’t risk messing with electricity.
There may also be risks involved with using the equipment, so staff, and anyone who could come close to the equipment (including children) need to be warned and trained. Workers using machinery and equipment can be entangled, have body parts severed or slip and fall near equipment.
Ask yourself, ‘Could the people around me or can I get injured when operating the machine?’
If the answer is yes, read up on machine safety for operators first. This article is a good introduction, https://www.safework.nsw.gov.au/your-industry/manufacturing/publications/machine-safety-operators, but by no means does it cover everything. Consult a professional or workplace safety HR consultant if you are unsure or need advice.
Posted in Farmer Advice
You Might Also Like
Jul 23 2025
Low yields from wheat production? Here’s why.
For the past two decades, agronomists and farmers have been trying to solve the problem of low yields using Variable Rate Fertilisation application. However, yield is only half of the equation. In-field…
Read MoreMay 25 2025
Get more from your livestock data with these six agtech solutions
Farmers across Australia are producing more data than ever. But much of it remains frustratingly siloed. Here’s how you can get the most from your data as a livestock producer.
Read MoreMay 20 2025
Purchasing AgTech? Ask yourself these five questions first.
Whether it’s your first time, or you’ve already got plenty of technology in operation – asking the right questions ensures you take the best approach.
Read MoreApr 22 2025
Building farm data trust
At AgTech Finder we ask vendors to provide their data policies so that farmers can make informed choices about agtech and be comfortable about the way their data is being collected and…
Read MoreList your company on AgTech Finder.
AgTech Finder helps Australian Farmers and producers find the product that’s right for them.
Register now to be a part of the community, get access to a national platform and start gaining insights to improve your products.